
Comment est-il fabriqué ?
- 1 four - 80 tonnes par jour - 14 000 tonnes par an
- 1 ligne d'assemblage automatisée + ligne semi-automatique flexible - Max 4M d'isolateurs.
- 1 ligne automatisée de revêtement par pulvérisation RTV.
- Laboratoire accrédité ISO 17025
- Plus de 150 employés dans la business unit
Composants de l'isolateur de suspension
- Diélectrique : Un diélectrique en verre trempé aux propriétés et à la forme appropriées pour les caractéristiques mécaniques spécifiées et les conditions environnementales dans lesquelles il doit fonctionner.
- Cap : Un capot en fonte galvanisé à chaud. Il est marqué de notre marque "ESA" et des autres marques gravées et encrées requises par les normes applicables pour assurer une identification correcte et une traçabilité individuelle.
- Tige : Une tige en acier forgé galvanisé à chaud. Elle peut être avec une bague de zinc anticorrosion (anode sacrificielle) sur demande. Cette bague en zinc est fortement recommandée pour les isolateurs destinés à être utilisés dans des environnements fortement pollués.
- Ciment alumineux : Le capot et la tige sont assemblés sur la pièce de verre à l'aide du ciment alumineux ayant les propriétés appropriées pour résister aux efforts thermomécaniques.
- Goupille : Enfin, le capot de l'isolateur est doté d'un dispositif de verrouillage en acier inoxydable (goupille) qui fixe les unités liées.
FABRICATION DE DIÉLECTRIQUES
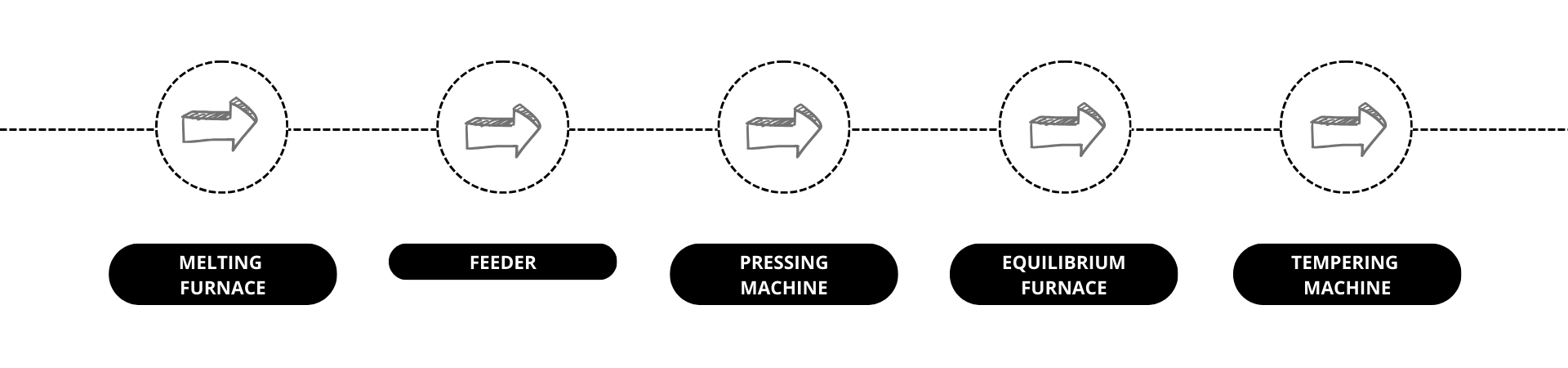
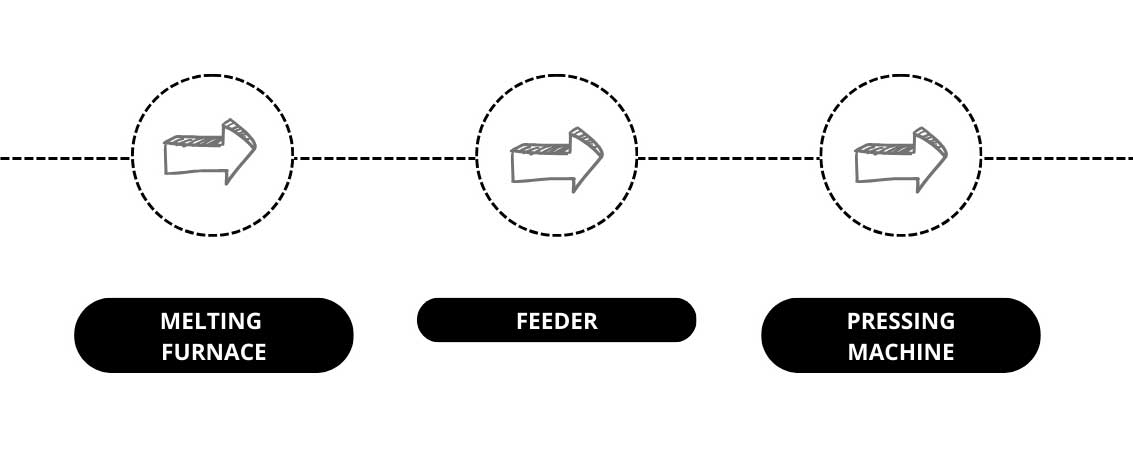
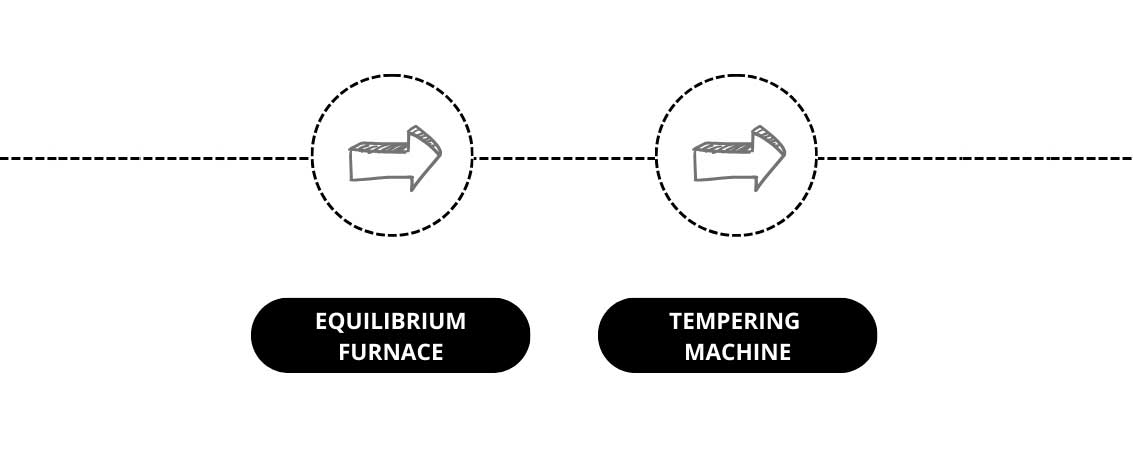
- Four de fusion : La matière première est introduite dans le four pour être fondue, puis on la laisse passer à travers le canal d'alimentation pour transporter le verre du four à la machine de pressage.
- Feeder : Ses fonctions sont de transporter le verre vers la presse, de conditionner le verre en température et, dans sa partie finale, de distribuer les portions de verre à produire. Une fois que nous avons obtenu une portion de verre déterminée par le modèle à produire, un mécanisme de lame sera utilisé pour la couper/séparer de la masse du canal d'alimentation. Grâce à ce processus, le verre tombera par son propre poids dans les moules qui seront placés dans la presse.
- Presse : Au moyen d'un système de pressage hydraulique, nous conformons la forme de la pièce de verre (diélectrique). Après ce processus, le verre est conditionné en température pour pouvoir être trempé. S'il n'est pas possible d'assurer la température correcte, les pièces sont introduites dans un four d'équilibre pour équilibrer la température de toutes les parties de la pièce.
- Four d'équilibre : Pour s'assurer que l'ensemble de la pièce de verre a une température homogène, le 100% de ces pièces passent par un four d'équilibre avant d'être trempées.
- Machine de trempage : Dans cet équipement, nous générons des tensions dans le verre. Ces tensions sont essentielles pour garantir que le diélectrique résistera aux contraintes de traction et de compensation auxquelles il sera soumis dans les lignes d'alimentation.
CHOCS THERMIQUES
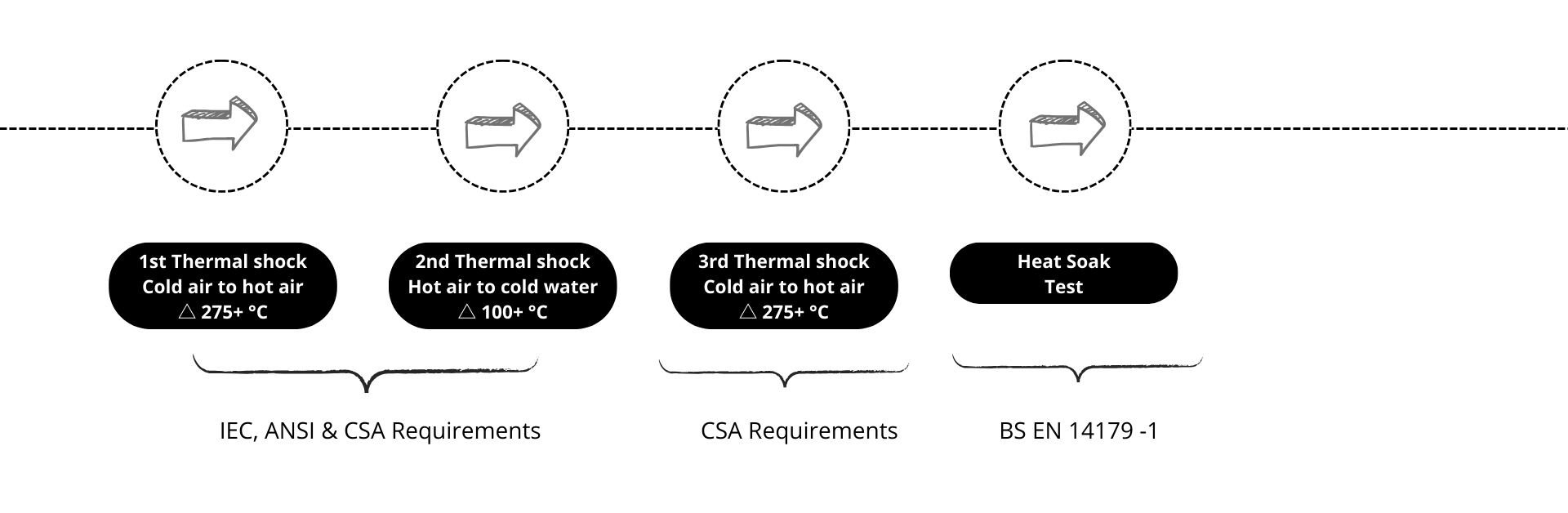
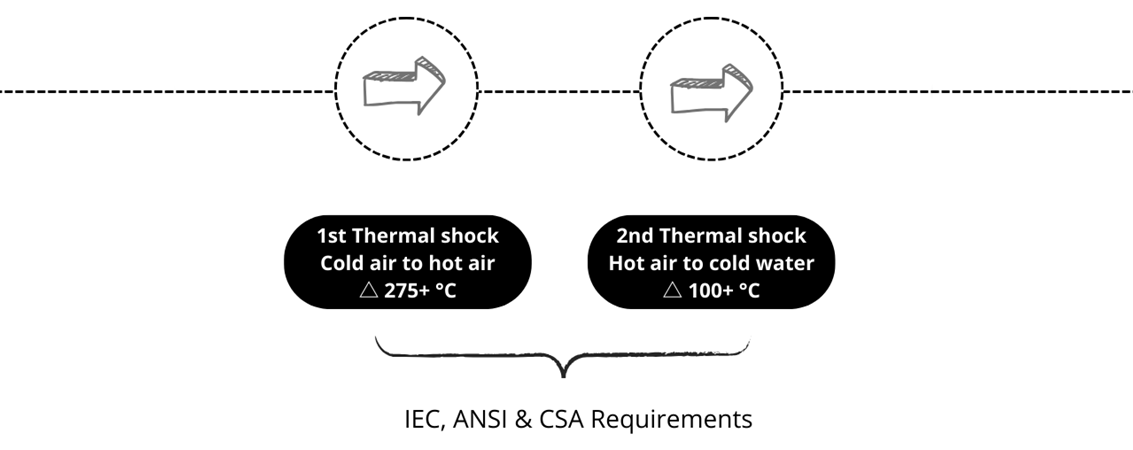
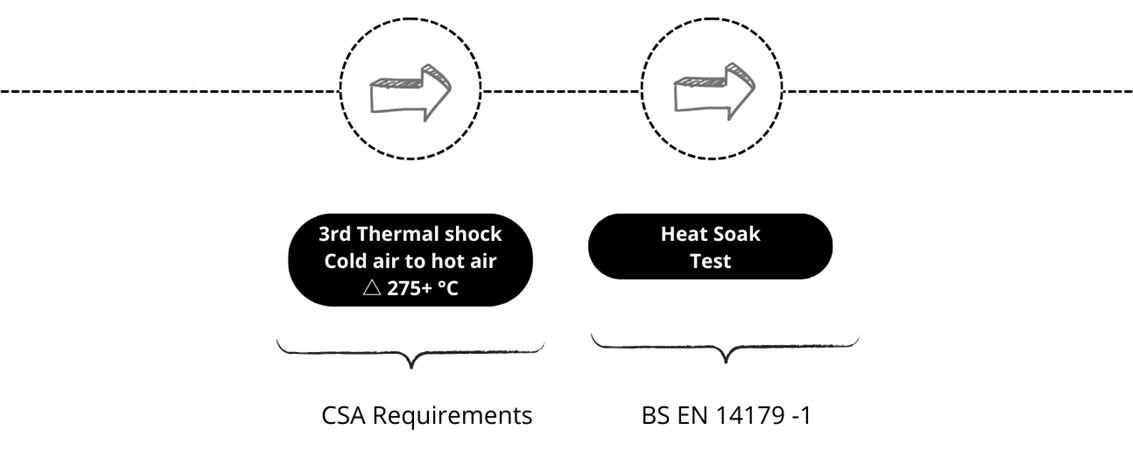
Avant d'être assemblées avec leurs composants métalliques, toutes les pièces en verre trempé sont soumises à une série de chocs thermiques dans le cadre d'essais de routine, comme suit :
- Choc entre le froid et le chaud : Chaque pièce en verre trempé est rapidement portée de la température ambiante à une température supérieure d'au moins 300 °C et maintenue à cette température élevée pendant au moins 1 minute.
- Choc entre le chaud et le froid : Chaque pièce en verre trempé est rapidement et complètement immergée dans de l'eau à une température ne dépassant pas 50 °C ; les pièces ont été préchauffées à l'air chaud ou par d'autres moyens appropriés à une température uniforme supérieure d'au moins 100 °C à celle de l'eau.
- Choc entre le froid et le chaud : Le choc thermique froid/chaud visé au point a) est effectué une seconde fois.
- Heat Soaking : Afin d'éliminer tout risque d'explosion par des inclusions de sulfure de nickel (qui peuvent provoquer l'éclatement du verre après la production de l'isolateur), après le deuxième choc thermique froid-chaud, chaque pièce en verre trempé est maintenue à 250 ºC pendant 2 heures.
ASSEMBLAGE D'ISOLATEURS
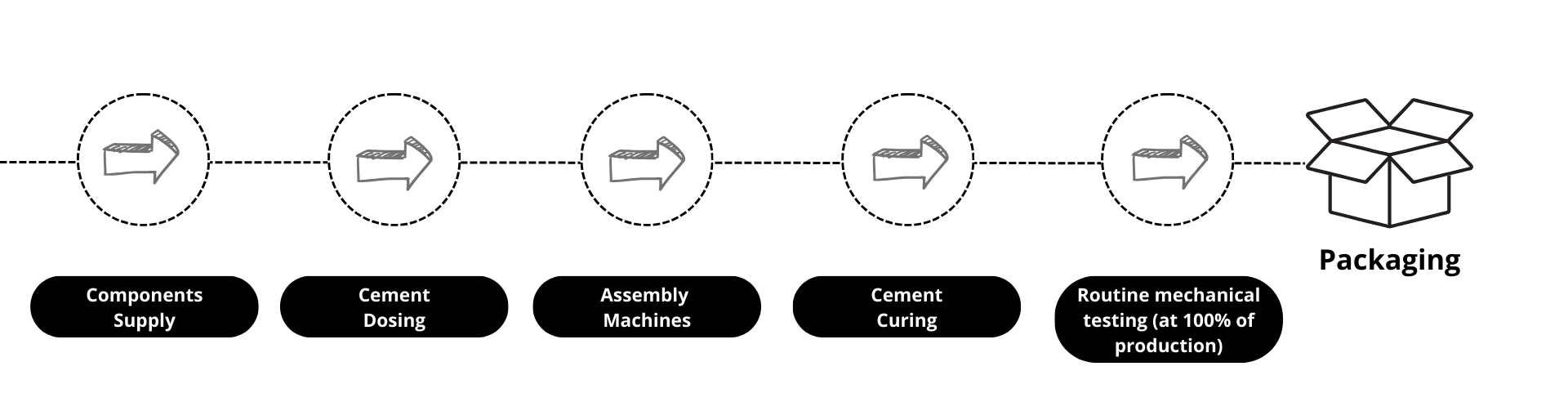

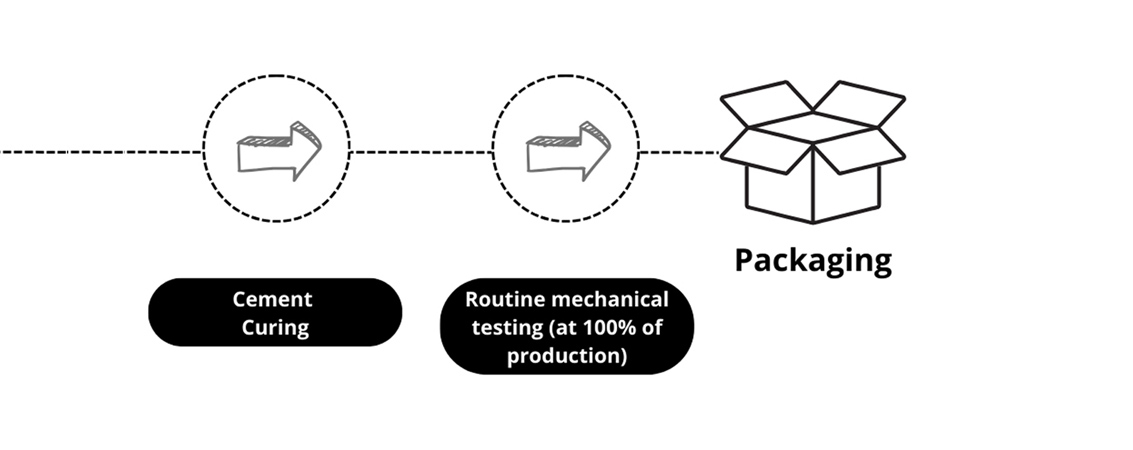
- Alimentation en composants : : Au cours de cette première étape, les composants nécessaires à l'isolateur en verre sont achetés et vérifiés, ce qui inclut généralement le diélectrique, le capot, la tige et la goupille.
- Dosage du ciment :Le ciment est soigneusement dosé pour garantir un assemblage correct. Il agit comme un agent de liaison qui maintient les parties de l'isolateur ensemble. Nous utilisons toujours du ciment alumineux, qui et insensible à la dilatation.
- Machines d'assemblage : Les pièces de l'isolateur sont assemblées dans des machines spécifiques qui appliquent le ciment de manière homogène et assurent une liaison solide. Il s'agit de fixer le capot et la tige sur le diélectrique.
- Durcissement du Ciment : Après l'assemblage, les isolateurs sont placés dans un réservoir d'eau de durcissement où le ciment durcit et la stabilité des liaisons est assurée. Le temps et les conditions de durcissement sont déterminants pour la résistance finale de l'isolateur.
- Essais mécaniques de routine (jusqu'à 100% de la production) : Chaque isolateur assemblé est soumis à des essais mécaniques et inspection visuelle de routine qui garantit sa qualité et sa solidité. Cela permet de s'assurer que chaque isolateur est conforme aux spécifications de conception et qu'il peut être utilisé en toute sécurité dans les applications électriques.
- Emballage : Une fois que les isolateurs ont passé les tests de qualité, ils sont emballés de manière appropriée pour être distribués et livrés. L'emballage doit protéger les isolateurs contre les dommages pendant le transport et le stockage, et comprend souvent des mesures de sécurité pour éviter que le verre ne se brise.